Pneumatics and electrics pump coal tar from 32 feet; recover 11k gal. over 3 yrs.
Thick, viscous, oily and sticky -- coal tar tops the list in contaminated site remediation and source recovery when it comes to stubborn and ugly cleanup, especially if there is lots of the stuff. Because of the difficult nature of coal tar, initial recovery efforts were skimpy and sporadic at the 30-acre Calhoun Park Area Superfund Site in the historic harbor district of Charleston, S.C., until site managers brought in a Blackhawk Anchor Electric piston pump to replace pumps that were performing poorly.
The Anchor was successful in steadily removing sinking DNAPL coal tar, prompting purchase of three additional Blackhawk Anchor Electric and Atlas Pneumatic pumps. Over three years, the Blackhawks pumped more than 11,000 gallons of coal tar from substrate at depths to 32 ft. below grade.The coal tar that has been removed is the byproduct from a manufactured gas plant that operated at the Calhoun Park Area Site from 1855 to 1957. The use of coal gas became obsolete with the widespread availability and lower cost of natural gas. The aboveground facility was demolished, yet the coal tar residues below surface remained.
“An electric Blackhawk pump with electrical controls was used where at 32 feet. underground, the coal tar is extremely thick and heavy,” the remediation program manager said.. “An automated controller was utilized and adjusted to ensure a slow and controlled recovery rate of one minute every hour around the clock. A second automated electric pump was added to a coal tar recovery trench. These pumps have worked for us very well given the conditions, and we have recovered on average three 55-gallon drums of coal tar per month from both wells.
"We’re also pleased with the results we’ve had with our two Blackhawk pneumatic piston pumps. In order to tackle other areas of the site, our contactor dug a trench around the perimeter, where we move the pneumatic pumps from well to well to recover coal tar from 15 to 20 feet below the surface."
An added benefit of choosing the Blackhawk pumps in an urban environment is because the piston pumps do produce fugitive emissions and air is not vented back into the well. Therefore there is no smell in the city air. The above-grade drive motors ensure that workers have minimal contact with liquid being pumped and that the pump discharge air is free of contaminants.
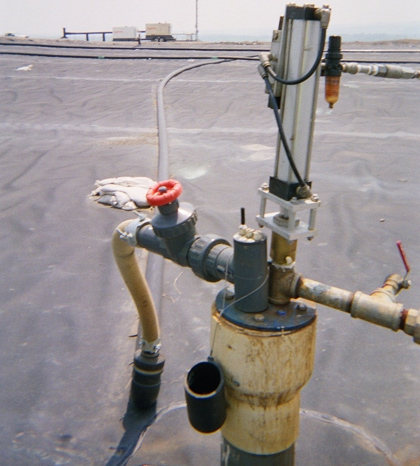
The Atlas Pneumatic pumps coal tar and other heavy hydrocarbons.
"We’ve had impressive, consistent and reliable pumping results with Blackhawk pumps, and a challenge or two along the way. When cold weather hits, coal tar is practically impossible to pump. By placing heat tape on the pump along with a drum heater, this problem has been alleviated," the manager said.
"We’ve also learned that because the tar is so thick, oily and sticky, the pneumatic pumps have to be cleaned every night for top performance the next day and, due to the viscosity of the coal tar, the seals have to be replaced. The great news is that despite encountering a few glitches here and there, we’ve got everything under control and when there is not enough tar material left in the well to fill the pipe, we’ll have a job well done."
Blackhawk’s electric and pneumatic piston pumps act like a syringe to extract product from the bottom of the well with each stroke. Because the pump inlet is at the bottom of each pump, liquid is pulled into the pump intake and the pump operates consistently whether the pumping action is clean or dirty. The positive-displacement action resists slowdown or stoppage even in the most sticky or oily situations. There are few moving pump parts in the well to cause problems. The pump drive mechanism is positioned on top of the wellhead, so each pump is easy to install, inspect, trouble shoot, and maintain.