Compressing Matters
Looking at the use of compressed air with leachate and condensate pumps
By Mark Bertane
As seen in MSW Management Magazine
Talk with a seasoned landfill managing engineer about pneumatic power. Pneumatic was already on site when he or she arrived, pushing compressed air significant distances to make leachate and condensate pumps work.
Hardly unusual. It would be difficult to find a North American landfill that doesn't rely on compressed air. Pneumatic is old-shoe technology – go-to because it is familiar, understood, almost comfortable.
And yet . . . not ideal. As landfills become more complex, today's manager faces issues – and surprising opportunities – unforeseen when most sites were first developed. And, like a telephone cable in wi-fi times, the old and accepted pneumatic systems are showing their technological age and limitations. Sites now have the opportunity, or the requirement, to communicate, measure and monitor each wellhead and pump. This takes power that pneumatic systems can't provide.
If pumping is a necessity, and compressed air is the legacy power source, our savvy and cost-conscious manager may start to grumble – about expense, down time, vulnerability, immobility, emissions, inconvenience, and, most recently, the inability to meet the challenges of elevated-temperature zones.
Pneumatic Issues
The issues are many and well known: To create compressed air, a site must rely on electrically powered compressors and other equipment. Dryers and strippers are necessary to prepare and condition compressed air to be used by air-driven pumps.
Capital outlays are steep even before the first pump is purchased. A structure must be bult. One compressor alone can cost $30,000 or more for a 100-hp unit.
To get the power from the compressor to the pump requires that pneumatic lines be trenched in – immobile and expensive to reroute. Laying pneumatic lines in new cells is costly. System maintenance means downtime. Compressors, dryers and strippers must be taken offline.
Compressed-air will leak along the line – escaping joints, perforations and fittings from the compressor to the pumps. Lines are vulnerable to accidental damage from machinery. When compressed air carries a moisture load and encounters sags in the line, constriction builds. If the water freezes, pumping stops altogether.
Electrically powering the pneumatic power is expensive, too. A typical pneumatic site with a 100-hp compressor and two 30-hp compressors can consume more than $50,000 a year in electricity when running at capacity.
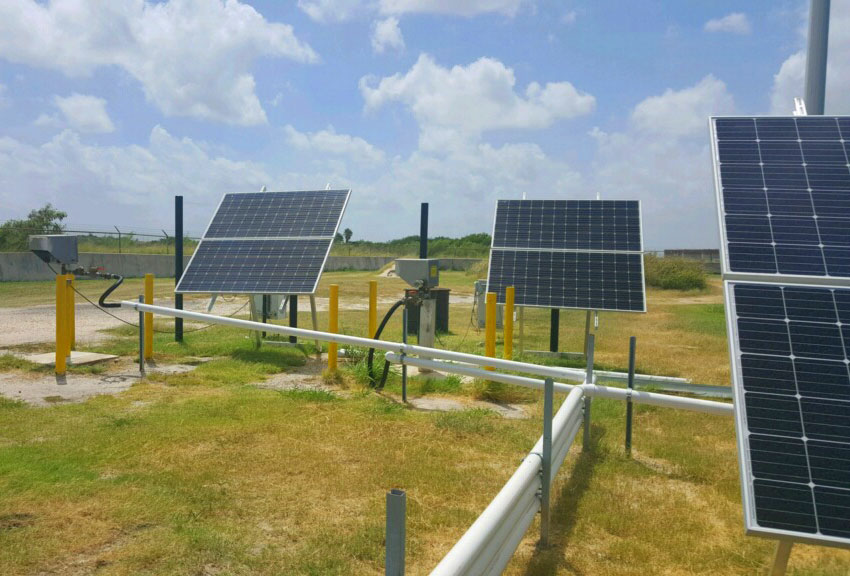
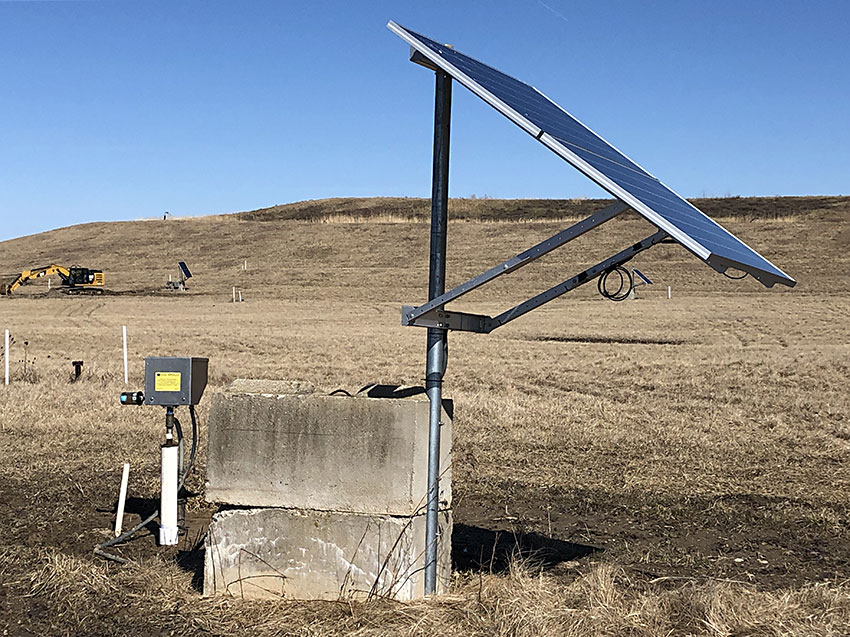
Poor Efficiency
Yet for all the work and expense of building and maintaining, the overall efficiency of a typical compressed-air system can be as low as 10-15%, making pneumatic one of industry's most expensive sources of power, according to the U.S. Dept. of Energy. *
To this system, often hundreds of pumps are attached, the great majority of which are air-drive submersibles. Because of their design, and despite strong efforts to update the technology, submersible air pumps face long-standing issues.
Principal among them is that the compressed-air power and the pumps' complex operational mechanicals (including a bundle of three down-well hoses) are submerged in toxic fluid of varying biochemical compositions. This creates environments that challenge pump integrity and force greenhouse gases to be vented into the atmosphere. Required maintenance means pumps routinely must be pulled from the leachate, a safety hazard for workers and a cause of more downtime.
Greater numbers of submersible air-driven pumps are failing or are notably incapacitated by factors ranging from unclean compressed air, to carbonate buildup, to elevated temperatures of zone liquids.
On the plus side, landfill technicians over time become well-versed on the intricacies of pneumatic systems and how to keep them running. The same was said of telephone-company repairmen.
Two Pumping Technologies
But let's assume our site managing engineer decides to make the best of the power infrastructure she or he inherited. Now the manager faces choices between two pump technologies to remove leachate and condensate.
The traditional air pump, long favored at most landfills, requires compressed-air power and the air-float actuator mechanism to be submerged in the landfill fluids. Compressed air flowing through the pump forces the fluids (and spent air) to the surface. Some of the spent air can leak into the discharge-fluid lines and piping (the manager can confirm this simply by metering discharge oxygen levels).
Oxygen and turbulence can help cause discharge pipes to clog with carbonite crystallization and/or to be blocked by air-lock bubbles that form in line high spots. Constricted discharge piping is recognized as one of the most common causes of pumping difficulties and incapacitation.
Another trending cause of pump failure is elevated temperatures, often in older, moister inner cells. Traditional air pumps, piping and tubing have been constructed using thermoplastic polymers that are not rated to withstand heat past 150° F. Over the past several years, ETLF zones have been reporting temps of 190° F and higher, with resultant shutdowns.
When compressed-air lines are in place and traditional air pumps fail, yet pumping is a necessity, our manager might consider another pneumatic technology – top-head drive, positive displacement piston pumps. The simple concepts of piston pumping drive water-well windmills and are most visible in above-ground oilfield pump jacks, with power and drive mechanics at surface level, safely distanced from the fluid being pumped.
Piston pumps today have been re-imagined, re-sized, improved and tailored to landfill and remediation/recovery sites. Advantages are many: Positive-displacement piston units pump virtually liquid, including viscous or foamy at any pH; operate at any angle, including horizontal; are unaffected by changes in positive or negative pressure; can run dry without harm; pump to the bottom of the well or sump independent of static head, and do not shear fluids. Because all power and drive mechanics are outside the well, compressed air does not contact the fluids being pumped so there is no contaminated exhaust air. Servicing is faster and less frequent, safer for workers.
A Different Power Option
But let's say our site is growing and the managing engineer needs to open a new cell or two. Or maybe the landfill is full and needs to close yet continue pumping. Maybe the pneumatic equipment is worn and needs replacement, or the lines have been damaged. Maybe the burden of pneumatic maintenance has become too much.
One answer is solar power. With reliability now well established in a variety of uses, solar panel prices steadily falling, battery-backup options increasing and the sun as a free-energy source, more landfills are turning to solar at latitudes as northerly as Toronto.
Paired with a simply designed above-ground piston driver, a solar pump with performance comparable to an air-drive submersible requires only one-fifth of the electric power needed for pneumatic systems – solar systems convert sunshine to direct current.
Prices for panels and related equipment have decreased more than 60% over the past decade, driven by technological improvements, the EnergySage solar marketplace reports.
Prices for panels and related equipment have decreased more than 60% over the past decade, driven by technological improvements, the EnergySage solar marketplace reports.
According to the National Renewable Energy Laboratory, the cost of solar panels decreased from $10/W to around $2/W, a decline of 80 percent from 1980 to 2010. The cost of solar panels dropped an additional 50 percent from 2015 through 2019, from $0.70/W to $0.35/W.
Panel installation in a landfill is relatively uncomplicated. A 300W panel is mounted roughly six feet from the wellhead. Panel maintenance is minimal – an occasional cleansing rainfall helps.
Linear-rod drivers employ the same, simple down-well piston-pump technology as pneumatic and electric drivers, and, with as few as four above-ground moving parts, feature infrequent servicing requirements. And rapid advances in battery technology promise to extend the working parameters of solar pumping.
An Engineer’s Perspective
A significant advantage is that solar pumps can be installed in remote locations without the need to trench pneumatic or electric, an attractive proposition for new cells and closed sites.
"The biggest factor for me about solar is the ability to move it from well to well and not have to run new lines," says one landfill engineer, who has installed solar pumps at his Midwestern landfill. "I like the fact that nearly all mechanical parts are above grade and not in the leachate," making servicing simpler and safer.
"I also like that parts are pretty interchangeable from pump to pump and you are able to build up older solar pumps with newer technology. Something small, but I don’t have to replace a whole system when I need a repair."
Solar is clean and green, with no exhaust gas vented into the atmosphere -- "a contained system that powers itself," according to the engineer – a technology in step with our time.
Pneumatic power’s future? It’s up in the air.
Mark Bertane is the principal executive of Blackhawk Technology Company
pump.info@blackhawkco.com
*https://www.energy.gov/sites/prod/files/2014/05/f16/compressed_air1.pdf